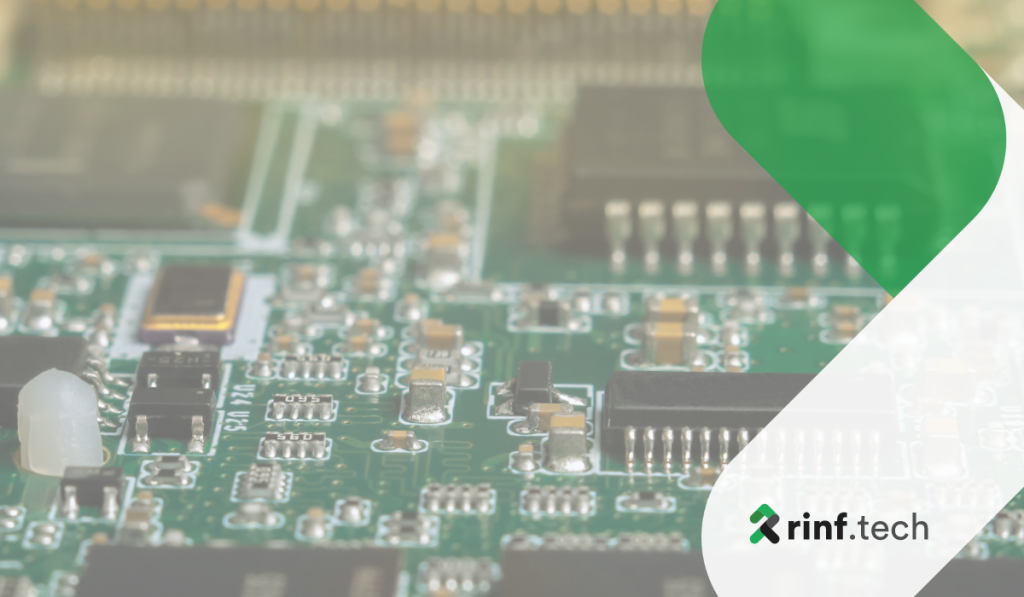
Fostering Innovation: R&D’s Role in Embedded Engineering
Exploring the pivotal role of R&D in driving innovation and digital transformation within embedded engineering.
Industrial automation affects almost every industry and economic sector in the modern world. Automation systems increase the production and efficiency of key economic activities such as engineering, construction, manufacturing, and power generation. Today’s industrial automation is seeing a new, major developmental boom driven by cutting-edge technologies like big data, cloud computing, artificial intelligence (AI), Internet of Things (IoT), and others.
This article explores the various aspects of industrial automation, from its definition to its far-reaching impacts on multiple industries. Companies and decision-makers can make more informed choices when implementing industrial automation solutions by understanding its benefits, challenges and limitations, and technologies behind it.
The term “automation” describes a wide range of technologies, techniques, and instruments used to minimize the need for human intervention in processes, increasing their productivity, efficiency, speed, and error-free nature. Automation has become indispensable in our daily lives, encompassing an expansive range of applications from household appliances and consumer items to sophisticated and intricate systems that power contemporary vehicles like ships and airplanes, factories, and even banking services.
Automation can be achieved by combining several scientific techniques and approaches—mainly mechanical, hydraulic, electrical, electronic, pneumatic, and computer—typically combined.
Mechanizing industrial processes and machinery is the primary focus of industrial automation. Information technology, specialized hardware (such as logic controllers and different kinds of modules), and robotic systems are used to support quality control, material logistics, and production processes to achieve this goal.
It is undeniable that automation affects many industries and supply chains in the modern world. A manufacturing facility or production assembly line without industrial automation technologies and instruments is becoming a rare sight.
Solutions for industrial automation enable 24/7 operation, dramatically speeding up production processes. Automated systems aren’t restricted by the physical or regulatory constraints on working hours that apply to human labor.
Industrial automation enables a streamlined workflow, reducing bottlenecks and improving overall process efficiency by automating repetitive processes. Furthermore, real-time monitoring made possible by automation helps optimize resources and lowers production downtime.
Product quality and consistency are greatly enhanced through automation, guaranteeing that each operation is carried out precisely. High-precision sectors like aerospace, pharmaceuticals, and automotive manufacturing need this consistency.
When properly programmed, automated systems are less prone to errors. Due to the significant reduction in the possibility of human mistakes, flaws, and inconsistencies, a better level of quality is maintained.
By managing risky jobs like heavy lifting, working in high temperatures, and handling toxic materials, automated systems can drastically lower the chance of occupational injuries.
Safety regulations can be met by programming industrial automation systems to shut down in case of mistakes or malfunctions. This guarantees the industry complies with regulations, protecting against possible legal problems and mishaps.
While automating processes can be expensive initially, significant labor cost savings will be saved over time. Automation makes labor more predictable and enables systems to be designed with a smaller labor budget as they become more efficient.
Automation guarantees a more economical use of resources by cutting waste and expenses. Everything is preserved in the production process thanks to automated systems’ exact measurement and use of raw materials.
Scalability is one of the best features of industrial automation. The organization may stay ahead of innovation by integrating new systems or updating old ones more easily as technology advances.
Automated systems are easily scalable, allowing them to adjust to changing market conditions. As a result, businesses are better equipped to react to any changes in the market, including unexpected orders and seasonal changes in demand.
Automated systems provide real-time data, and this can be very helpful for making decisions. This data may contain production rates, efficiency levels, and error reports, among other indicators.
Businesses with fast access to trustworthy data may improve short-term tactical planning and long-term operations by making well-informed decisions.
Companies that provide industrial automation services have a higher chance of surviving in a market that is becoming increasingly competitive. Automation offers the speed, efficiency, and quality necessary to compete successfully.
Organizations can more easily adjust to changes in the market thanks to industrial automation. Reprogramming automated systems to perform multiple tasks gives manufacturing more flexibility.
A company’s carbon footprint can be considerably decreased by optimizing automated systems for energy consumption. Machines can be configured, for instance, to enter a low-power state when not in use.
On average, automated systems generate less waste—material scraps, energy waste, or emissions—by running more effectively. This is better for the environment as well as saving money.
The high initial cost of the equipment, software, and skilled personnel is one of the biggest obstacles to the widespread adoption of industrial automation. Automated system setup frequently requires expensive, complex network settings, specialized hardware, and cutting-edge software.
Although automation might save costs in the long run, small and medium-sized businesses may need help to justify the initial investment due to the immediate financial strain. The amount of time required to see a return on investment could vary, and this phase of economic recovery may act as an obstacle for many companies considering switching to automation.
Many components, including sensors, actuators, and control systems, are used in implementing industrial automation, and they all must coordinate. These sophisticated systems require specific expertise for installation, upkeep, and troubleshooting.
Integrating new technology can be difficult for businesses using manual processes or outdated automated systems. Issues with data management, software interoperability, and hardware compatibility frequently make this a multifaceted challenge.
A team of professionals skilled in programming, system monitoring, and data analysis is required for industrial automation. Companies based in places with a shortage of skilled workers sometimes need help.
Businesses frequently need to engage in extensive training programs to get their current staff up to speed on new automated technologies. In addition to requiring more funding, this also involves a transitional period where production could decline.
The fear of automation-related job losses frequently sparks resistance from labor groups and workers. While automation can result in displacing specific jobs, it also creates new roles requiring different skills. This change is surrounded by complex social factors that call for careful treatment.
The public perception that automation eliminates jobs has grown significantly, impacting how quickly businesses implement new automated systems. Persuading internal and external stakeholders of the long-term advantages of automation can be difficult due to deeply held beliefs.
The foundation of modern data analytics and industrial automation decision-making is artificial intelligence (AI). Artificial Intelligence (AI) can analyze large volumes of data to find patterns, forecast outcomes, and make decisions in real-time using machine learning algorithms.
AI integration into industrial automation can be complex, needing a lot of processing power and specialized knowledge. But the advantages—like quality control and predictive maintenance—often exceed the drawbacks. Businesses offering industrial automation services progressively integrate AI into their solutions to obtain a competitive advantage.
PLCs, or programmable logic controllers, are industrial digital computers, especially for managing production operations. They are essential in collecting sensor data and converting it into machine-readable commands.
PLCs’ versatility and scalability are one of their advantages. Because PLCs are a flexible option for businesses investing in industrial automation technology, they can be easily adapted to accommodate the needs of growing or changing operations.
Operators communicate with the automated system through Human-Machine Interfaces or HMIs. Projecting control options and data visualizations onto screens enables human operators to monitor and manage automated operations.
Efficiency and safety can be negatively impacted by how simple it is for operators to navigate and use the system, which can be significantly influenced by the HMI’s design and intuitiveness. Inadequate HMI design might result in lost productivity and operational mistakes.
Industrial robots are used for various jobs, including painting, inspecting, and assembling. They are most frequently encountered in manufacturing, outperforming human workers at dangerous, repetitive, or precision-based jobs.
In addition to being programmable, modern industrial robots have artificial intelligence (AI) capabilities and sensors that allow them to learn from and adapt to their environment. Their versatility makes them perfect for various industrial applications beyond simple repetitive activities.
SCADA systems are crucial to industrial automation because they enable the monitoring and controlling of various remote assets from a single location. They provide quick, data-driven decision-making by gathering real-time data from multiple sensors.
SCADA systems need to be highly secure because they manage crucial industrial processes. Since they are frequently the target of cyberattacks, cybersecurity is vital when using SCADA in industrial automation.
Distributed control systems, or DCS, are typically used for complex processes inside a single location, such as a manufacturing facility, in contrast to SCADA systems, designed for large-scale, wide-area control. DCS provides a high degree of dependability and redundancy.
Real-time manufacturing process optimization is possible with DCS systems, which can modify several factors to increase productivity, quality, and safety. They frequently work with other methods, such as PLCs and HMIs, to provide industrial automation from a holistic perspective.
IIoT refers to the interconnection of industrial systems and devices for data collection, analysis, and action. It is frequently regarded as the key technology that makes contemporary industrial automation possible.
IIoT solutions scale quickly to handle increased numbers of data points and devices. Scalability also brings security and data management issues, which call for solid solutions for successful applications.
Digital twins provide a real-time view of a system’s performance as virtual copies of the real thing. Predictive maintenance, system optimization, and even the remote control of automated systems is made possible by this.
By simulating various operating situations, digital twins enable engineers to evaluate improvements in a virtual environment before implementing them in the real system. This makes it possible to make better-informed decisions and lowers the risks of changing the system.
Instead of sending data to a centralized data center, edge computing in industrial automation processes data at or close to the location of data development. As a result, automated systems can make decisions more quickly and with less delay.
Although edge computing enables faster responses, its computational capacity could be inferior to centralized systems. All the same, the trade-off often results in substantial improvements in productivity and lower running expenses.
Industrial automation incorporates immersive technologies like virtual reality (VR) and augmented reality (AR) for maintenance, training, and remote operation.
While these technologies have many exciting possibilities, there are drawbacks, such as high costs and the requirement for specialized skills to create and maintain immersive environments.
Hardware-in-the-loop (HIL) testing involves using real-time simulations to test the hardware components of an automated system. This type of testing is critical for systems where failures can result in significant damage or risks to human safety.
We at rinf.tech worked with a global manufacturer specialized in agricultural equipment to optimize their testing processes. In hardware-in-the-loop (HIL) testing, the hardware components of an automated system are tested using real-time simulations.
The results speak for themselves: successful testing of 2 ECUs on a standard test bench, 35% automation coverage, and a 40% boost in testing capabilities. Our ongoing assistance helps the client make strategic financial and operational decisions.
In the automotive industry, automation is widely used for jobs including welding, painting, assembly, testing, and inspections. High-quality standards are maintained while productivity is maximized by accurate and efficient operations made possible by advanced robotics and sensor technologies.
Automation is essential for packing, testing, soldering, and assembling tiny and delicate electronic components. Reducing errors and increasing production speed are made possible by computerized quality checks and high-speed assembly lines.
Automation and IoT devices are crucial in precisely applying water, fertilizers, and pesticides.
For instance, we at rinf.tech developed the Thermal Vision ToughBook for one of our clients. This solution enables thermal imaging to assess plant health and irrigation needs, significantly improving crop yield and sustainability.
Drones and automated harvesting equipment boost efficiency by quickly covering huge areas while reducing the need for human labor. A more timely and consistent harvest is made possible, essential for crop quality.
The processing of agricultural products is made faster and more accurate with automation in the sorting and packing processes. By sorting them according to size, color, and quality, fruit and vegetable waste can be significantly decreased using advanced vision systems and machine learning algorithms.
Automated systems keep an eye on the health and welfare of cattle, sending out early warning signals for any problems that require treatment. To ensure the animals are in excellent health, this can involve monitoring their movement, temperature, and even their biometrics.
Automated systems handle tasks like sorting, cutting, packing, and labeling. High-speed conveyors and robotics ensure that food products are processed and packed more quickly and cleanly than would be possible by human hands.
Advanced vision systems and sensors are implemented to inspect product quality and conformity to standards. Real-time data analytics help in the immediate identification of quality issues, leading to less waste and higher consumer satisfaction.
Processes, including drug formulation, testing, and advanced screening, are accelerated by automation. Robots can simultaneously carry out thousands of trials, speeding up research and reducing development expenses.
Sample analysis uses automated equipment, guaranteeing great diagnostic accuracy and speed. This is especially important in urgent medical situations where a prompt diagnosis might significantly impact the patient’s prognosis.
Automated seismic surveys and robotic drilling technologies are used for effective resource exploration. Automation makes extraction operations quicker, safer, and more effective. This is especially useful in challenging conditions like deep-sea drilling.
Automated control systems effectively handle the intricate operations of processing and refining. Real-time monitoring raises yield and lowers waste by ensuring the systems run within ideal parameters.
Automated picking and packing systems improve order fulfillment accuracy and speed. Large stocks can be managed by robotics and conveyor systems, guaranteeing precise and timely deliveries.
Automated and robotic storage and retrieval systems (AS/RS) are employed for effective inventory management. These systems have a better turnover rate and use of available space because they can run continuously.
Automation provides accurate and safe control over exact chemical reactions, mixing, and processing. Real-time process variable adjustments are possible using sensors and controllers, guaranteeing ideal conditions for every response.
The generated chemicals are guaranteed to meet the necessary quality standards via automated testing. This is essential for regulatory compliance as well as for profitability.
Automated systems optimize the generation, distribution, and monitoring of energy. They control the complex interactions between various energy sources and their distribution channels, maximizing efficiency and reducing costs.
Automation is crucial in efficiently managing and maintaining renewable energy sources like solar panels and wind turbines. Sensors and controls can adjust the positioning of these installations in real time to capture the most energy.
Automation is essential for the exact assembly and thorough testing of aerospace components. Automated systems ensure that every part satisfies strict quality and reliability criteria, which are necessary given the significant safety requirements in this industry.
Automated systems are used for maintenance and inspection work. Advanced imaging technology and robotics can do intricate jobs that are challenging, time-consuming, and potentially dangerous for human workers.
The efficiency and security of mineral extraction and processing activities are increased with automation. It makes it possible to adjust to changing material properties more quickly, which optimizes the extraction process.
Systems for automated inspection guarantee that the materials under processing fulfill quality standards. Large volumes of mined material can be accurately and quickly graded for quality using high-definition cameras and sensors.
As new technologies develop and work together, industrial automation is set to undergo even more significant changes in the future. Thanks to artificial intelligence and machine learning development, automation systems can make judgments, anticipate faults, and even optimize themselves. Furthermore, it is predicted that the rise of 5G connectivity will significantly expand the Industrial Internet of Things (IIoT) capabilities, resulting in more efficient real-time control and communication.
Edge computing is another trend set to revolutionize industrial automation by enabling data processing closer to where it is generated. This can result in more efficient use of bandwidth and faster reaction times in automated systems. Cyber-physical systems (CPS) are also becoming more prevalent, enabling a tighter confluence of computational and physical processes, resulting in more adaptive and robust automation solutions.
Integrating quantum computing with automation may offer unparalleled computational power, leading to breakthroughs in complex tasks like material science simulations and optimized logistics. Moreover, the increasing affordability of sensor technologies may lead to more widespread adoption of automation in sectors that need to be faster to adopt it, like small-scale manufacturing and local agriculture.
Another prospective development is the integration of blockchain technologies to ensure data integrity and security within automated systems. This can be particularly beneficial in sectors requiring high levels of traceability and compliance with stringent regulatory requirements. Human-robot collaboration is also expected to increase, with more intuitive interfaces and smarter robots that can learn from human behavior.
By leveraging these partnerships, companies can share the risk and pool resources to develop groundbreaking technologies that might be too resource-intensive for individual organizations to pursue. This collaborative approach is crucial in tackling the complex challenges that the future of industrial automation presents, from ensuring cybersecurity to developing globally recognized standards and protocols.
As new technologies develop and work together, industrial automation is set to undergo even more significant changes in the future. Thanks to artificial intelligence and machine learning development, automation systems can make judgments, anticipate faults, and even optimize themselves. Furthermore, it is predicted that the rise of 5G connectivity will significantly expand the Industrial Internet of Things (IIoT) capabilities, resulting in more efficient real-time control and communication.
Edge computing is another trend set to revolutionize industrial automation by enabling data processing closer to where it is generated. This can result in more efficient use of bandwidth and faster reaction times in automated systems. Cyber-physical systems (CPS) are also becoming more prevalent, enabling a tighter confluence of computational and physical processes, resulting in more adaptive and robust automation solutions.
Integrating quantum computing with automation may offer unparalleled computational power, leading to breakthroughs in complex tasks like material science simulations and optimized logistics. Moreover, the increasing affordability of sensor technologies may lead to more widespread adoption of automation in sectors that need to be faster to adopt it, like small-scale manufacturing and local agriculture.
Another prospective development is the integration of blockchain technologies to ensure data integrity and security within automated systems. This can be particularly beneficial in sectors requiring high levels of traceability and compliance with stringent regulatory requirements. Human-robot collaboration is also expected to increase, with more intuitive interfaces and smarter robots that can learn from human behavior.
By leveraging these partnerships, companies can share the risk and pool resources to develop groundbreaking technologies that might be too resource-intensive for individual organizations to pursue. This collaborative approach is crucial in tackling the complex challenges that the future of industrial automation presents, from ensuring cybersecurity to developing globally recognized standards and protocols.
At rinf.tech, we have a full-fledged R&D Embedded Business Unit that specialises in custom software product engineering and proof-of-concept (PoC) project development. From computer vision powered intruder detection software to robotic arm and its digital twin to sophisticated deep learning models, we use experimental approaches and lessons learned to build top-notch solutions and prototypes to future-proof business ideas and emerging tech.
Exploring the pivotal role of R&D in driving innovation and digital transformation within embedded engineering.
This article will share three strategies to help R&D teams effectively and successfully implement new technologies.
Guiding manufacturers on how to implement digital twin technology, fostering an environment where production is not only streamlined but also more intelligent and responsive to market demands.
Copyright © 2023 rinf.tech. All Rights Reserved.
Terms & Conditions. Cookie Policy. Privacy Policy.
Politica Avertizari de Integritate (RO)