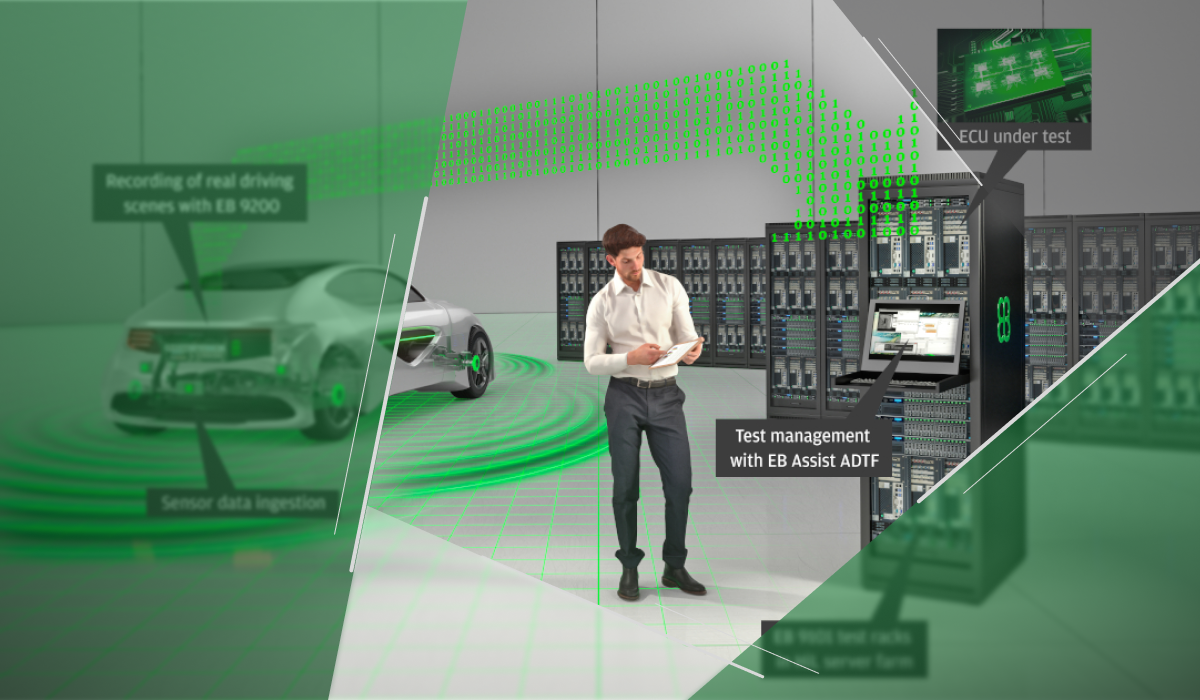
Hardware-in-the-Loop (HIL) testing is a simulation-based testing technique used in various industries to validate and verify the performance of complex systems. HIL testing aims to develop a virtual setting where essential hardware elements may communicate with digital simulation models. Before a system is deployed, HIL testing is used to assess the behavior and functioning of the system under test in a controlled and repeatable manner.
HIL testing aims to evaluate how a system’s hardware and software interact. Engineers can stimulate the hardware with fictitious signals produced by the simulation models by connecting physical components, such as sensors, actuators, and controllers, to a simulation platform. This enables them to assess how the system’s hardware reacts to various scenarios, outside factors, and inputs from the simulated software.
HIL testing has several benefits over conventional physical testing. It makes it possible to spot problems before they become severe and lowers the hazards brought on by system breakdowns. Without using pricey prototypes or deployment in actual situations, it also enables comprehensive testing economically. By adopting HIL testing, engineers may effectively validate complicated systems, enhance performance, and guarantee reliability.
HIL testing is a methodical procedure for thoroughly testing and validating complex systems. Here is an overview of the HIL testing process:
The first two steps in the testing process are understanding the system being tested and defining the test objectives. This entails identifying the system’s hardware and software components and their interactions. Determining the test cases, scenarios, and environmental variables that will be simulated during the HIL testing process is known as test planning.
Simulation models mimic the system’s software components’ behavior. These models provide artificial signals that simulate the software’s inputs and outputs. The simulation models are created using specialized software programs, and they’re intended to faithfully replicate the behavior of the actual system under various operating circumstances.
The HIL testing equipment is connected to hardware components, such as sensors, actuators, controllers, and other devices. The hardware must be interfaced with the HIL testing platform, which serves as the main control system. The connections may consist of communication interfaces, analog and digital inputs and outputs, and any interfaces necessary for testing the system.
The test cases are run while integrating the hardware and simulation models. The activity of the software components is mimicked by the simulation models, which provide artificial signals that activate the actual hardware. These signals are received by the hardware components, which then produce outputs that are monitored and transmitted back into the simulation models for analysis.
Data from the hardware elements and simulation models are gathered and examined during the test. This entails keeping track of and recording the hardware’s responses, contrasting them with the expected behavior, and spotting deviations or anomalies. Data analysis tools and algorithms assess the system’s functionality, interactions, and performance under various test scenarios.
After the test execution, the findings are recorded in a test report. The report includes information about the test cases, measured data, analysis findings, and any concerns or suggestions that were found. The system design, simulation models, or test cases are modified or improved as necessary due to the findings. To improve the system and ensure its performance complies with the intended specifications, the process could involve iterating through the test planning, model creation, and test execution stages.
It is also important to mention that the HIL testing platform consists of hardware and software components. The hardware connects the simulation models and the actual hardware components through signal conditioning units, I/O interfaces, and communication interfaces. These interfaces handle data interchange, convert analog to digital signals, and synchronize simulation models with hardware.
HIL testing systems use test automation and simulation technologies on the software side. The program must run the simulation models that simulate the behavior of the software components. It produces fabricated signals that serve as the software’s inputs and outputs. The test automation program creates, runs, and manages the test cases. It enables engineers to set up simulation models, design desired test scenarios, keep track of the test execution, and evaluate the outcomes.
This refers to the actual hardware, such as sensors, actuators, controllers, and other devices, that make up the system being tested. These elements communicate with the simulation models using the HIL testing setup.
These are computer-based representations of the system’s software parts’ behavior. The software’s inputs and outputs are represented by synthetic signals created by the simulation models. During testing, these signals are employed to excite the fundamental hardware components.
The HIL Testing Platform is the testing setup’s central control system. It acts as an interface between simulation models and actual hardware components. The platform monitors and gathers data, exchanges signals between the hardware and the simulation, and permits closed-loop communication between real-world objects and the simulated environment.
They are designed, carried out, and managed using test automation tools. It enables engineers to set up simulation models, design desired test scenarios, and keep track of test execution. Software for test automation also offers resources for reporting and analyzing test results.
Communication and input/output (I/O) interfaces make it easier for simulation models and real hardware to interact. The simulation platform and hardware components can communicate signals and data thanks to these interfaces. They could consist of serial and Ethernet interfaces, analog and digital inputs and outputs, and additional communication protocols for the test system.
Hardware and simulation models must be carefully considered while implementing HIL testing. Identifying hardware parts compatible with the system being tested and can faithfully simulate its behavior is crucial. This entails choosing sensors, actuators, and controllers that adhere to the system’s specifications and performance standards. Additionally, the hardware must have enough I/O interfaces and communication protocols to connect successfully with the simulation models.
The choice of simulation models is equally important for precisely portraying the software-based parts of the system. Based on the functional and behavioral needs of the system, the models should be created or selected. They should faithfully reproduce the behaviors and interactions of the software parts, supplying reliable data to the hardware and enabling precise evaluation of the hardware results. To ensure the correctness and dependability of the simulation models, proper validation and verification must be carried out.
The implementation of HIL testing has its own set of difficulties and restrictions. Real-time performance is among the difficulties. HIL testing needs the simulation models to run in real-time, feeding hardware with inputs and quickly assessing the outputs. Especially for complicated systems with high computing needs, ensuring that the hardware and simulation models can run simultaneously and satisfy the real-time requirements can be challenging.
The complexity of developing and maintaining precise simulation models presents another difficulty. It can take a lot of effort and resources to create simulation models that accurately reflect the behavior of the software components. Although crucial, model validation, verification, and calibration can be difficult due to the scarcity of available reference data or the system’s complexity.
HIL testing helps to improve system performance and dependability. HIL testing identifies areas where the system is weak or vulnerable by putting it through various operational situations, environmental factors, and failure scenarios. Engineers can then make the necessary adjustments and optimizations to increase reliability. HIL testing also helps assess the operation and performance of the system and its parts to ensure they adhere to the required requirements.
HIL testing enables engineers to adjust the system’s behavior, refine control algorithms, and boost overall performance by modeling complicated interactions between hardware and software components. Early problem identification and correction increases system robustness and aids in producing high-quality goods.
When a global agricultural equipment manufacturer faced a challenge, they turned to rinf.tech for a solution. The company had to choose between a novel, unproven alternative for ECU testing and a well-known, production-tested HIL automation system. They also required a standard testing platform for numerous ECUs and a more in-depth internal expertise to effectively set the HIL bench gear. They needed to be more restricted in their ability to spend money on new HIL bench components. Their internal IT team’s communication issues further hampered their operations.
To overcome these challenges, rinf.tech offered a thorough V-model approach to the optimization of the software testing process. Our team created a brand-new HIL environment from the ground up for manual and automated testing, created HIL for automation testing, and used Siemens Polarion to standardize validation procedures. Using the scripting languages Python and CAPL, they also produced automated testing.
With the use of a single standard test bench, the client was able to test two ECUs successfully. By adding more test cases, they could reach 35% automation coverage, and by improving the support for test case development and automation procedures, they could expand their testing capabilities by 40%.
HIL testing is commonly used in industries where complex system development and validation are essential. The automotive industry is one of the main sectors where HIL testing is frequently used. HIL testing is crucial in the automotive engineering industry for validating electronic control units (ECUs) and their interfaces with various vehicle subsystems. It enables engineers to mimic numerous driving scenarios, climatic variables, and fault states without requiring actual prototypes. As a result, the development process is sped up, automotive systems are guaranteed to be reliable and safe, and physical testing is less expensive and time-consuming.
HIL testing is also used in other sectors, such as aerospace. Avionics, flight control, and communication systems all use it to test their operation and effectiveness. Engineers can assess these systems’ performance through HIL testing under various flying circumstances, disturbances, and failure scenarios. In doing so, it helps to ensure the safety and dependability of aviation systems by assisting in the early detection and correction of any problems.
HIL testing is also essential in power systems and energy industries. The effectiveness and stability of electrical grids, power-producing machinery, and renewable energy systems are all verified using this method. HIL testing aids in power system design optimization, reliability improvement, and efficient operation by simulating the behavior of various components and testing the system’s reaction to varied load circumstances.
HIL testing is a favored choice for many companies since it has several advantages over conventional testing techniques. The capacity of HIL testing to simulate complicated and realistic operating situations is one of its main benefits. HIL testing enables engineers to simulate various scenarios and environmental elements that may be challenging or expensive to replicate in physical testing by fusing real hardware with simulation models. This comprehensive testing capability enhances the system’s overall performance and dependability.
The cost-effectiveness of HIL testing is another important advantage. HIL testing eliminates the need for pricey prototypes and the accompanying maintenance costs compared to physical testing. Because the tests are carried out in a controlled virtual environment, it reduces the chances of equipment destruction or damage during testing. By spotting and fixing problems early, HIL testing facilitates quicker and more effective development cycles, reducing time-to-market and lowering costs.
Compared to physical testing, HIL testing offers more consistency and reproducibility. Test cases may be duplicated and adjusted in the simulation environment, enabling consistent and standardized testing techniques. As a result, comparing and evaluating the system’s performance over various test iterations is more straightforward because the findings are dependable and consistent.
HIL testing also makes it possible for comprehensive and scalable testing. Engineers can run a lot of test cases and variations that cover a variety of failure situations and operational settings. This level of extensive testing aids in discovering possible problems, designing optimization, and improving the overall performance and safety of the system.
Several new technologies and breakthroughs are anticipated to impact the future of HIL testing. Artificial intelligence (AI) and machine learning (ML) are two trends increasingly used in HIL testing procedures. Vast amounts of data collected during HIL testing can be analyzed by AI and ML algorithms, which can then be used to find trends and make defensible conclusions. This can aid in automating the creation of test cases, improving test settings, and enhancing fault isolation and identification. AI and ML can also help with predictive maintenance by detecting early failure based on ongoing data analysis.
Future developments and uses for HIL testing in numerous industries are possible. HIL testing will be essential in developing autonomous vehicles in the automotive industry. HIL testing will be essential for confirming the interactions between the vehicle’s sensors, control algorithms, and actuators as autonomous systems become more complicated. HIL testing will help ensure ADAS‘s dependability and safety (advanced driving assistance systems).
Scalability and adaptability will be the primary areas for improvements in HIL testing procedures. HIL testing frameworks must change to support more extensive and varied system configurations as complex and interconnected systems become more prevalent. Seamless interoperability will be made possible by creating standardized interfaces and protocols, simplifying the integration of various hardware and software components.
Hardware-in-the-Loop (HIL) testing is a valuable and effective method with many advantages for developing and testing products. Its importance comes from its capacity to deliver a thorough, accurate testing environment that mixes essential hardware elements with simulated software behavior. Increased testing effectiveness, shorter development times, lower costs, risk reduction, and improved system performance are just a few benefits of HIL testing.
Organizations from various sectors are advised to consider including HIL testing in their plans for testing and developing new products. Companies can gain a competitive edge by accelerating time-to-market, lowering costs, and improving the reliability and performance of their systems by utilizing the advantages of HIL testing. HIL testing will be increasingly crucial in guaranteeing the resilience and functionality of various goods, from automotive systems and avionics to energy grids and industrial automation, as technology develops, and systems become more sophisticated.
In this article, we’ll explore the current Ops landscape, why unifying these disciplines through XOps is so powerful, how to implement XOps successfully, and how it can unlock new levels of enterprise agility.
Exploring the pivotal trends defining enterprise software development in 2024 and beyond.
Exploring the strategies and critical considerations for enterprises venturing on digital transformation journeys through application modernization.
Copyright © 2023 rinf.tech. All Rights Reserved.
Terms & Conditions. Cookie Policy. Privacy Policy.
Politica Avertizari de Integritate (RO)